The development of inspection and maintenance programs for industries such as oil and gas is an involved process that requires significant resources including input from a variety of stakeholders such maintenance engineers and planners, operators, and contractors.
“The best-laid plans of mice and men often go awry.”
– Robert Burns, To a Mouse, 1875
Plans often go awry…
Robert Burns’ observation about plans often going awry applies equally to established inspection and maintenance programs. In real life, there are plenty of reasons why it might be necessary or beneficial to deviate from an established inspection or maintenance program, such as:
- Resource Constraints: Limited availability of personnel or equipment to perform maintenance tasks can force the deferral of maintenance tasks.
- Prioritization: Immediate operational demands or more urgent projects may take precedence over previously scheduled tasks.
- Supply Chain Issues: Disturbances in supply chains can cause spare parts to become scarce or unavailable.
- Changing Economics: The cost of parts or labour can change over time, impacting the cost effectiveness of a particular maintenance strategy.
Deferrals are not Consequences-Free
Although there may be good reasons to defer inspections or maintenance, each time a task is deferred there is a potential for increased risk, such as:
- Asset Deterioration: The lifespan of assets can be shortened, leading to the need for more frequent repairs, replacements, and higher capital expenses.
- Reduced Efficiency: Equipment or facilities that are not properly maintained may operate less efficiently, leading to reduced throughput and higher costs.
- Safety Risks: Delaying maintenance and inspections can increase the risk of equipment failures that can lead to accidents with unacceptable consequences to human health or the environment.
The Importance of Having a Process
We can all appreciate that there can be legitimate reasons for deferring inspection and maintenance tasks, and that changes to those programs can increase risk. For those reasons, it is critical that a process is put into place to document, review, approve, and communicate changes and deferrals in inspection and maintenance programs. Such a process should address some of the following concerns:
Accountability and Transparency
An effective process can ensure that every decision made regarding changes and deferrals can be traced back to its origin, providing a clear audit trail. Keeping track of who decided and why helps ensure that all stakeholders understand their roles and contributions.
Planning and Scheduling
Documenting changes and deferrals helps in the accurate allocation of resources, ensuring that personnel, equipment, and finances are used efficiently, and that critical maintenance tasks are prioritized.
Risk Management
Documentation allows for the identification and assessment of risks associated with deferred maintenance, helping to mitigate potential negative impacts. By understanding what has been deferred, organizations can develop contingency plans to address potential failures or urgent maintenance needs. A properly documented change and deferral process can ensure that any regulatory requirements are satisfied.
Performance Monitoring
Keeping track of changes and deferrals can provide data that can be used to benchmark maintenance performance against goals and industry standards, and to feed into future maintenance planning and decision-making processes.
Analyzing documented changes and deferrals helps identify areas for improvement in the maintenance process, contributing to continuous improvement efforts.
In summary, having a process for documenting changes and deferrals in inspection and maintenance programs ensures that maintenance activities are managed systematically and effectively. It supports accountability, communication, planning, risk management, cost control, performance monitoring, compliance, and informed decision-making, contributing to the overall efficiency and effectiveness of maintenance operations.
Change and Deferral Process
Considering everything we have covered, it is obvious why we need a change and deferral process.
Below we show a simplified process where a change or deferral request is initiated by a Requestor, typically an operator, inspector, or a maintenance manager. The Requestor provides the details for the change and deferral request, including the scope, the potential risks, and stakeholders.
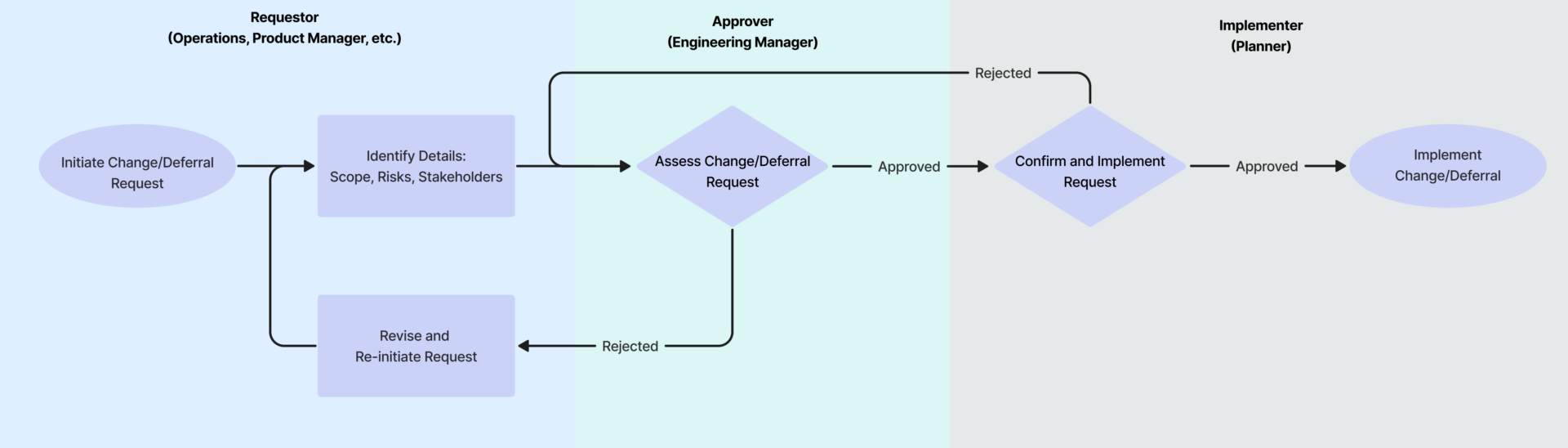
Next, the request is reviewed by an Approver, such as a maintenance engineer or engineering manager whose job it is to assess whether the identified risks are acceptable or not. From there, the request is either returned to the Requestor, if the details are not acceptable, or forwarded to the Implementer.
Implementors are typically inspection or maintenance planners whose job is to manage inspection or maintenance programs. If any issues are identified with the request, it is sent back to the Requestor and, if not, the request is approved and implemented.
The Details Matter
Inspection and maintenance programs in industries such as oil and gas are complex and resource intensive. Such programs require planning and input from various stakeholders, including maintenance engineers, planners, operators, and contractors. However, even the most meticulously planned programs may need adjustments due to resource constraints, competing priorities, and supply chain issues.
While deferring maintenance tasks might sometimes be necessary, such deferrals increase the risk of accelerated asset deterioration, reduced operational efficiency, and accidents.
Having a structured process for documenting, approving, and communicating changes and deferrals is crucial. Such a process enhances accountability and transparency, ensures efficient resource allocation, aids in risk management, and facilitates performance monitoring. It also supports compliance with regulatory requirements and contributes to the continuous improvement of maintenance operations.
Wrapping Up
We know that our best laid plans will often go awry. For this reason, a well-defined change and deferral process is important for maintaining the integrity and efficiency of inspection and maintenance programs. Such a process can ensure that all decisions are well-documented, that risks are managed, and that stakeholders are kept informed, leading to more reliable and safer operations.
By adhering to these practices, organizations can better navigate the challenges associated with maintaining their critical assets, ensuring long-term operational success and safety.
Looking for Change and Deferral Software?
Cenosco’s Integrity Management System software suite (IMS) includes integrated tools to help you manage changes and deferrals in your inspection and maintenance programs. Tools such as IMS PEI (Pressure Equipment Integrity), IMS RCM (Reliability Centered Maintenance) and IMS SIS (Safety Instrumented Systems) can take the pain out of documenting and reporting your inspection, maintenance, and monitoring data.
If you are interested in improving the inspection and maintenance processes at your facilities, Cenosco can help. Fill in the form below to schedule a demo!
Request a Demo
Want to see IMS in action? Explore our features such as Asset Hierarchy, Offline mobile functionality, 2D and 3D Capabilities and so much more.
Follow us on LinkedIn